Implementing Our
Core Value Framework
While the construction of Dundalk Shopping Centre was the Fastest Store build of its kind in the Tesco Estate world wide, the projects complexity offered additional challenges and opportunities & presents an excellent case study for our Core Values Framework.
Our Framework is designed over 6 Sectors, Environmental, People & Process, Community, Client, Financial and Technology.
With the implementation of our Lean Building Ethos, Precision Construction Limited have developed the Core Values Steering Wheel. This is a tracking document which sets measurable & achievable development targets across our building and fit out processes. The targets are set at Director level and are designed to challenge each department through innovation.
Each month the tracking document enables us to test & improve our building processes & review the results in order to capture & identify both positive & negative trends and adopt lessons learned.
Where applicable PCL will set and apply these targets to the fitting out and refurbishment works in co-operation with the clients own project targets.
Environmental Awareness
PCL set a Target to Recycle 95% or over of Recyclable Material, thereby Reducing Landfill Volumes.
13,397 tonnes of waste
was removed from the site
98.7% (13,222 tonnes)
of waste removed was recyclable
99.7% (13,186 tonnes)
was recycled
Environmental
Awareness
PCL set a Target to Recycle 95% or
over of Recyclable Material, thereby
Reducing Landfill Volumes.
With the success of our reduction in waste up to 90% on our Zero Carbon Supermarket in Cabra, we aimed to improve further on this in Dundalk. With demolitions starting in September 2013 our team on site have been diligent in reducing non recycled waste volumes throughout the project to ensure our target of 95% was achieved.
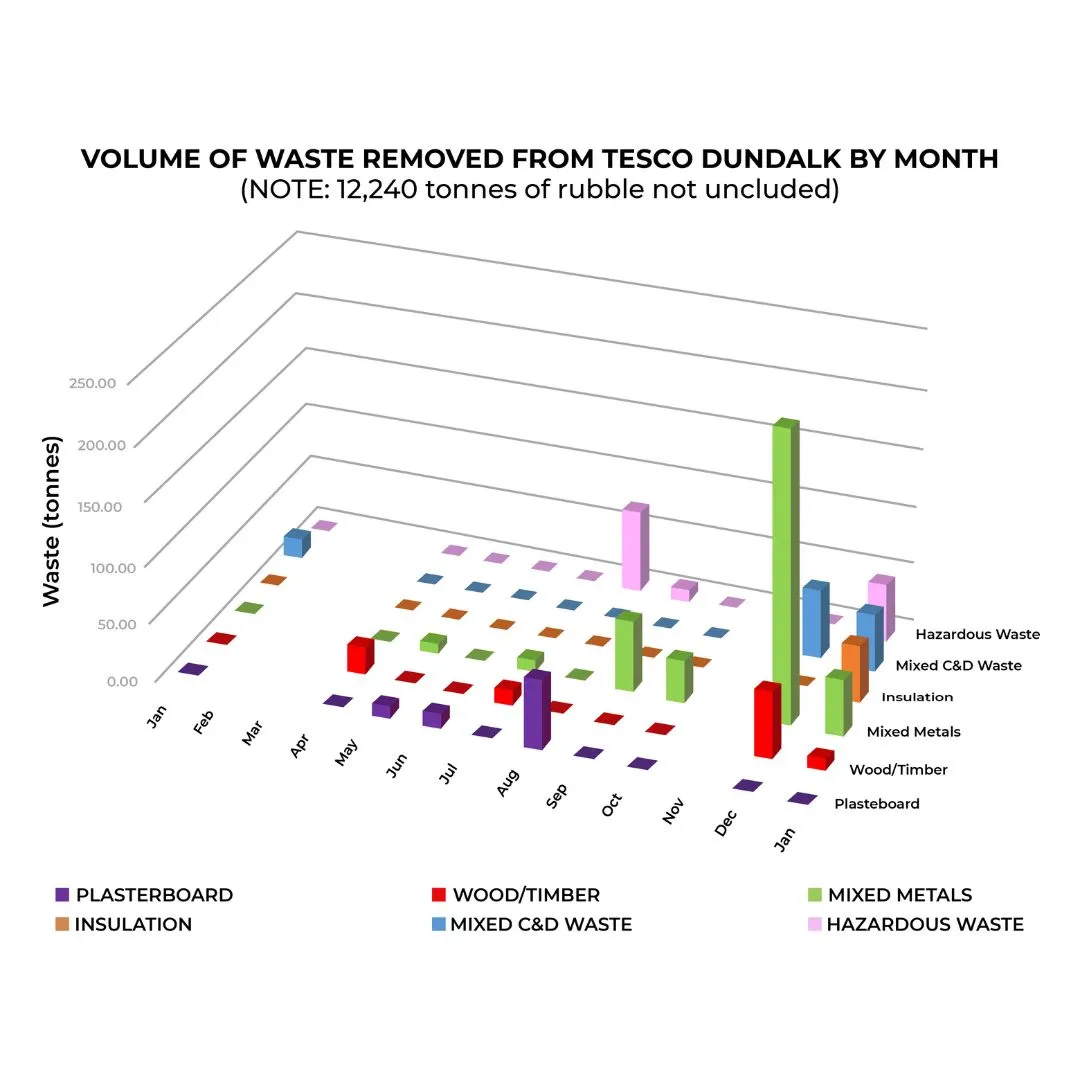
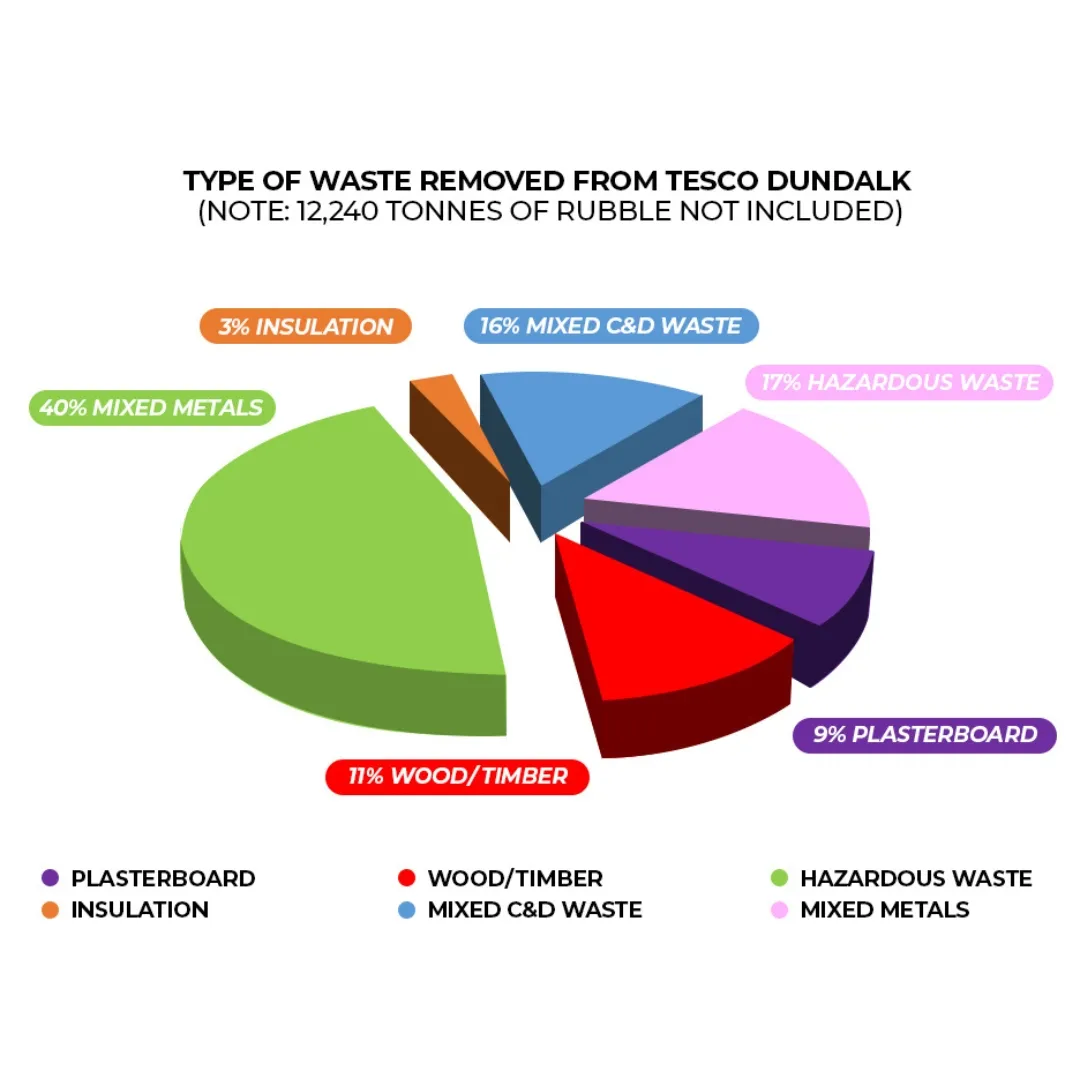
People & Process
local employment & upskilling
PCL set a Target to Employ 20% of its Directly Employed Workforce from the Local Area
Sourcing
Local Skills
PCL’s onsite staff is comprised of Site Managers, Coordinators, Engineers, Quantity Surveyors, Administrators, Site Operatives & Cleaning Staff. Of the 15 Direct Employees currently onsite, 11 are living locally.
Sourcing
Local Knowledge
The benefits of direct employment of local operatives and management has gone well beyond the social responsibility for community support.
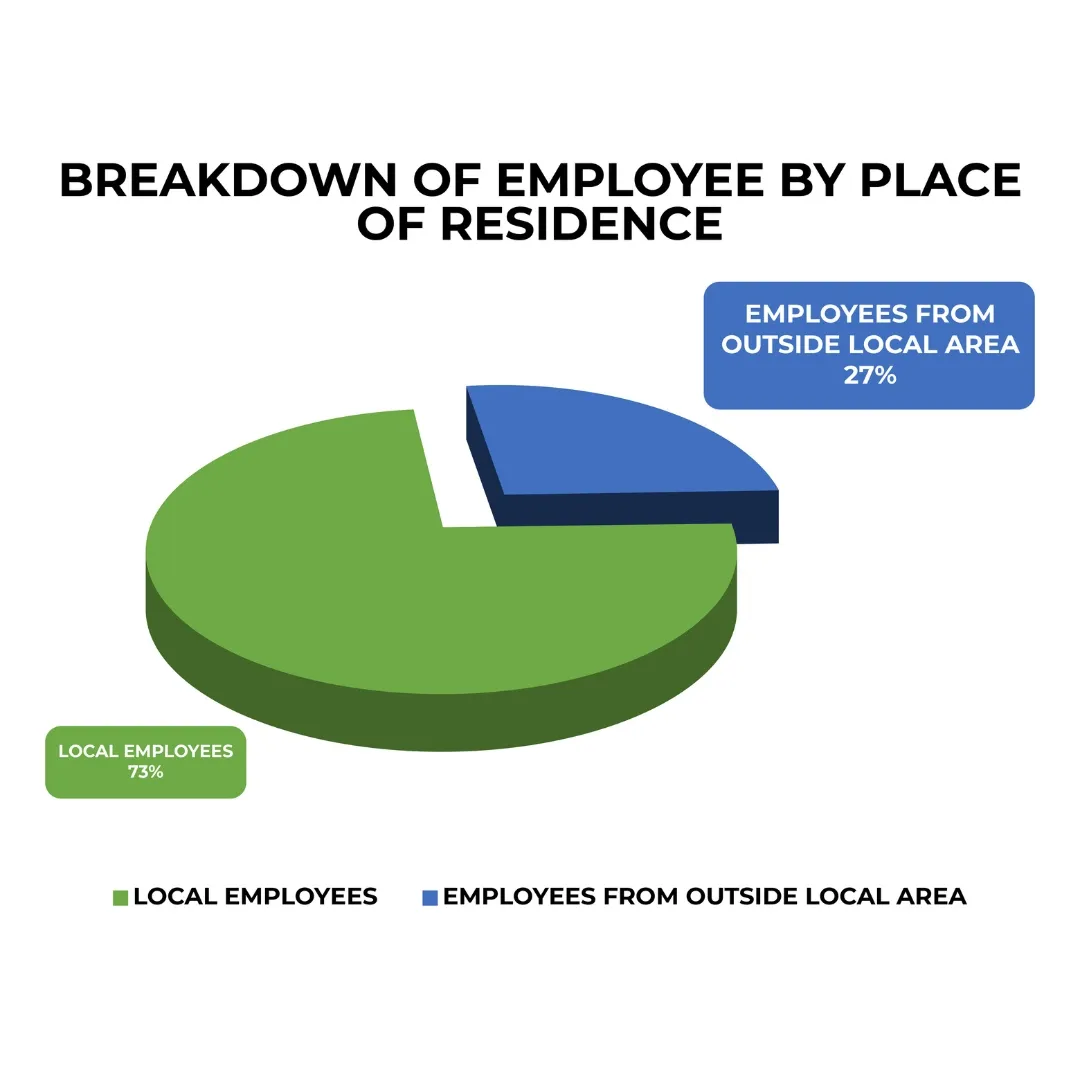
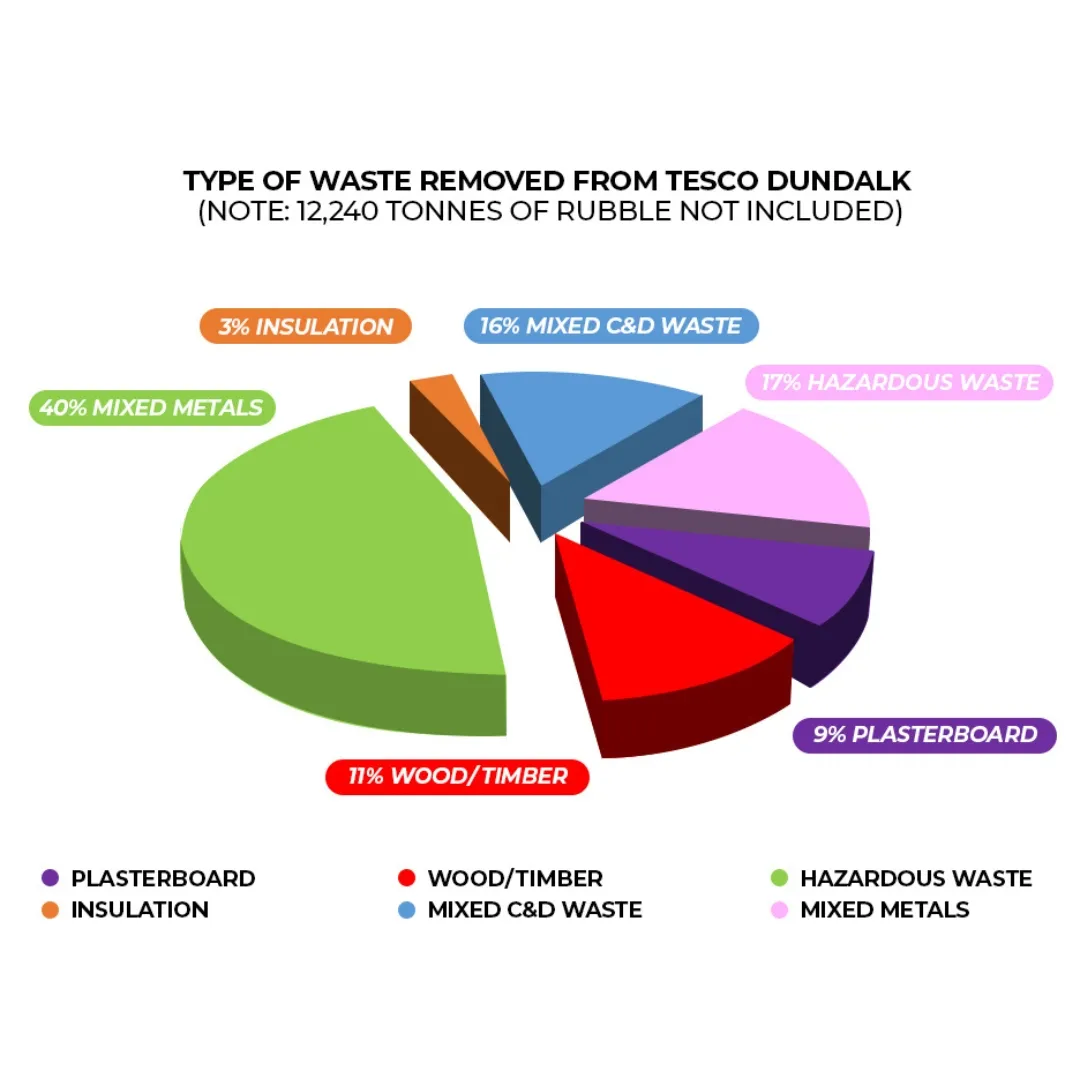
Engaging with local official’s and employment agencies enabled PCL to open up direct lines of communication regarding Fast-Tracking Aspects of the Development as there was a Complete Buy-In and Trust within the Dundalk community and associated organisations who benefited directly from the Redevelopment.
Community
Supporting Local Business
PCL set a Target to Source 25% of all Non-Specialist Construction Materials within a 50km radius of the Construction Site
We have achieved 35% of the Total Non-Specialist Construction Spend (6.3m) of the entire contract within a 50km radius of the Construction Site.

€6.3 million worth of non-specialist construction materials have been sourced within a 50km radius.
This equates to 35% of the total non-specialist construction spend of the entire contract.

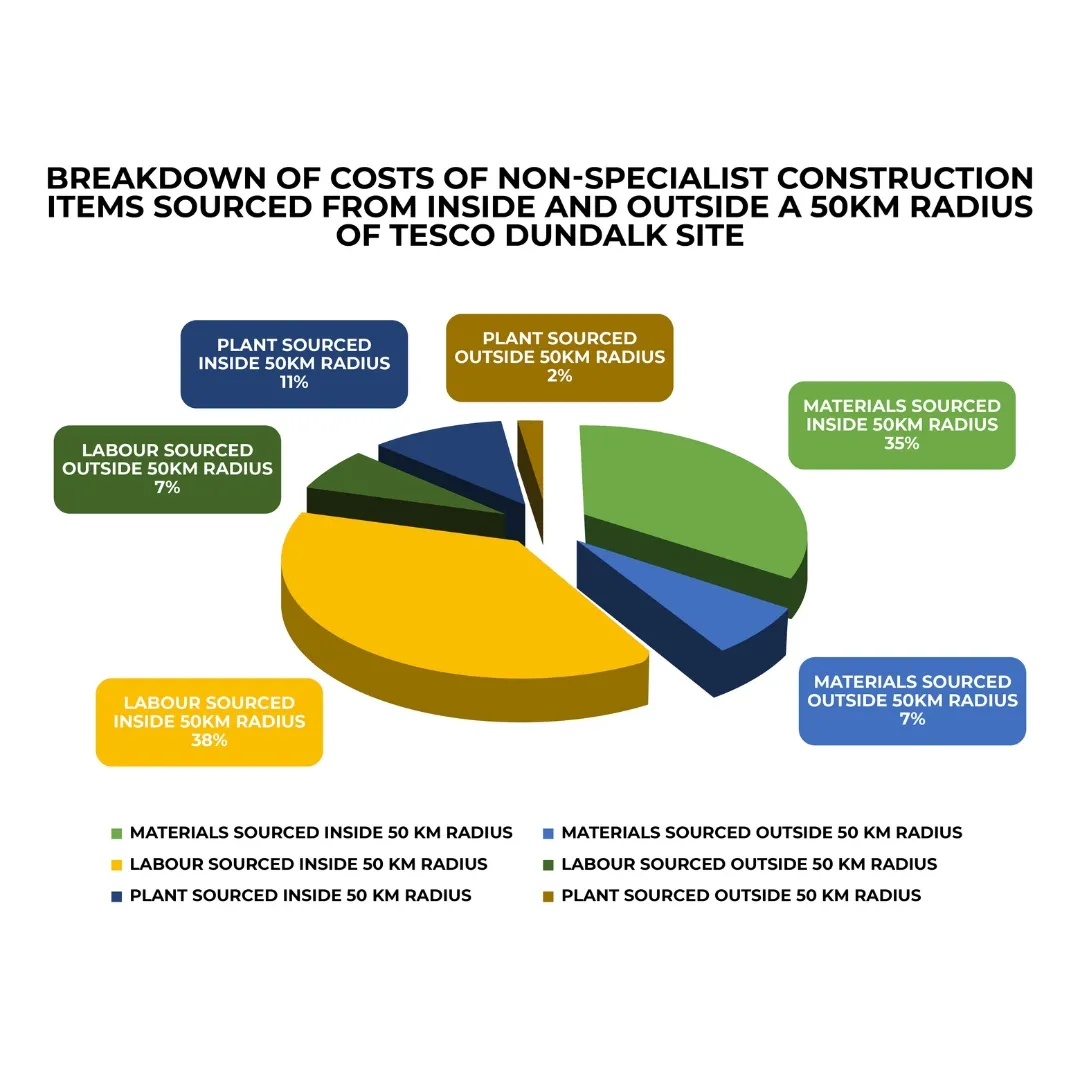
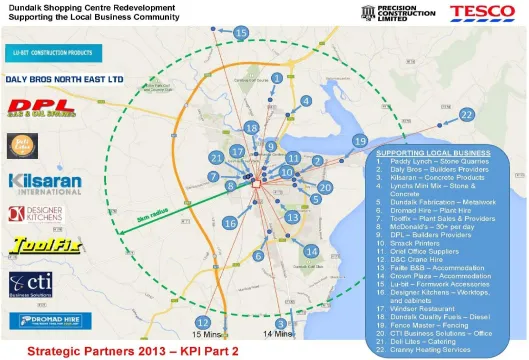
Technology
Looking
Forward
PCL’s innovation framework is built on the strong implementation of the most suitable People, Process & Technology for each project.
Target
PCL set a Target to Fully Implement a BIM Framework from Conception to Completion
What is BIM?
Building Information Modelling is a collaborative based building process run in conjunction with an innovative 3D Modelling Tool.
.webp)
The Collaborative System
Removing the barriers of the old hierarchy system, the collaborative system provides access for all disciplines at the early design stage of the project. This allows the design team to draw on the expertise of suppliers, fabricators installers etc. and capture the full knowledge of specialist contractors with up to the minute industry innovation & concepts from all stakeholders
BIM & 3D Modelling
With our Strategic Partners, Our 3D model is a real time virtual structure, expanding in detail as the information is uploaded and developed.
Stored in the cloud, this virtual structure can be accessed at any time by all team members and reviewed to provide measurements, details, quantities, costs, clash detection etc.
As the project develops the model can be transferred to Client data base as an integral part of the O&M Manuals and becomes part of the Health & Safety File.
.webp)
Initial designs capture specialist contractor innovation and concepts, reducing the risk of over design or redesign at a later stage.
The benefits of BIM
With the BIM system we obtain complete team involvement at the Design stage, our Strategic Team members are chosen based on past performance & reliability.
The BIM model provides a framework for integration and measurement before construction on site takes place. This means substructure, superstructure and fit-out elements can all be fully designed within one virtual structure, enabling earlier procurement, prefabrication, reduction in delivery and reduced construction & life cycle costs.
With Ireland's slow progression into the use of Building Information Modelling (BIM) PCL have embraced this technology early, complementing our proven lean construction, collaboration process and lessons learned from our strategic partnering teams/projects.
Financial
Client
Value
Independent Quantity Surveyors have carried out an audit on behalf of the Client and have benchmarked Tesco Dundalk against 3 of their current Tendered projects and the original E-Tendered rates of Tesco Cabra.
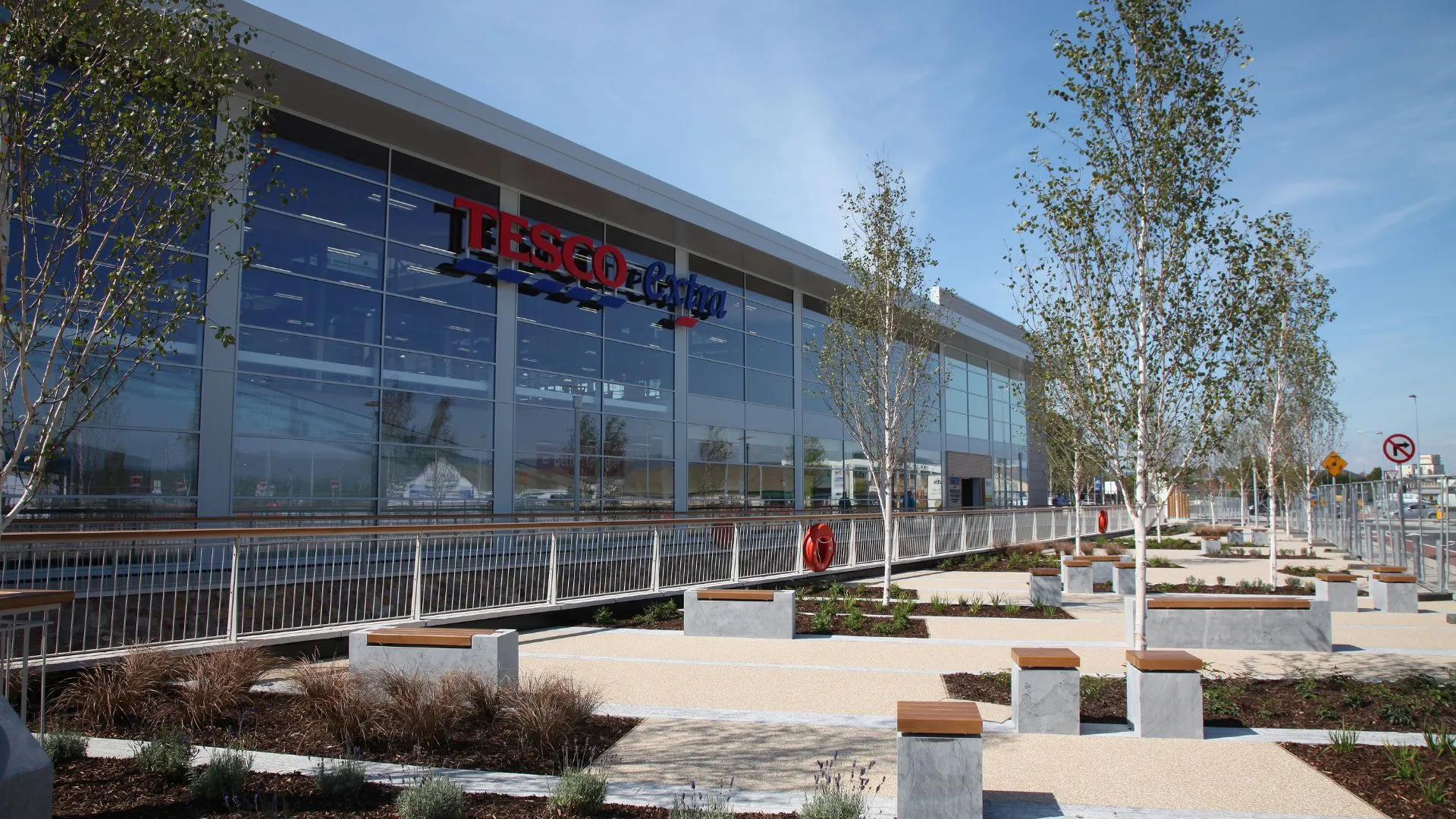
Value Engineering
& Project Savings
Critical Collaboration Factors which resulted in a more efficient Contract Programme
- Re-sequencing within Section E provided working areas earlier in programme & enabled better working continuity –ie. Mall and Ramp areas.
- Challenging the conventional sectional handover process by having multiple sections being constructed concurrently.
- Applying additional resources to achieve critical handover key dates.
- Implementation of BIM to reduce traditional design & signoff lead-times.
- Collaboration process has enabled the pre-ordering of up to 95% of the shell and core components.
- Pre fabrication of Fit-out elements, including package plant room, mechanical, electrical & sprinkler component assemblies.
- Sourcing of local storage facilities has enabled these components to be delivered to site as and when required.
Have a question?
leave your email & we’ll contact you directly